Cat® Large Dozers are common sights on mines and quarries around the world, serving as both primary and support tools in multiple applications. While they may look easy to operate, implementing specific techniques can help operators maximize the potential of their dozers.
Caterpillar continually makes engineering updates and incorporates new technology solutions to help customers get more value out of their investment in Cat dozers. And Caterpillar application experts and equipment trainers focus on compiling best practices and educating the people who operate them.
Operators are key to maximizing dozer efficiency, performance and productivity. Using the wrong techniques can significantly reduce overall productivity. It is critical that operators understand dozing best practices — and have the knowledge and skills to execute them. Even good operators can increase their efficiency by understanding basic application principles and specific dozing techniques.
DOZING APPLICATIONS
Dozers are ideal tools for a variety of applications — from production dozing to reclamation operations. They can be dedicated to waste dump operations, work on stockpiles and steep slopes, participate in haul road construction and perform ripping applications.
Whatever the application, Caterpillar application experts recommend the following general operating techniques:
- Always doze in first gear to ensure the blade is fully loaded and you’re using the full capability of the machine.
- Steer with blade tilt cylinders rather than steering clutches when the blade is loaded.
- Minimize corner loading, prying and impact dozing.
- Load the blade downhill and take advantage of machine weight and gravity.
- Maintain a steady dozing pressure.
- Keep unloaded travel distance to a minimum.
THE DOZING CYCLE
While there are dozens of best practices surrounding dozer operation, a good starting point is the dozing cycle itself. Should you doze front to back or back to front? Should you travel quickly with small loads, or move slowly with a large load?
Caterpillar application experts have studied multiple dozing scenarios and identified techniques that can make the dozing cycle more efficient and productive.
Back-Each-Pass Technique — Least Efficient
With this technique, the operator starts each pass at the back of the cut. Each pass uses the entire length of the cut at a uniform depth. Efficiency and productivity suffer because the machine travels the entire length of the cut in both directions with each pass.
“When you’re in reverse, you’re not being productive,” explains Corey Metz, a Caterpillar senior product consultant. “You’re creating windrows rather than actually digging down and creating a slot. You’re traversing a longer distance, not pushing downhill and there is a lot of spillage. As a result, this technique delivers the least productivity at the highest cost.”
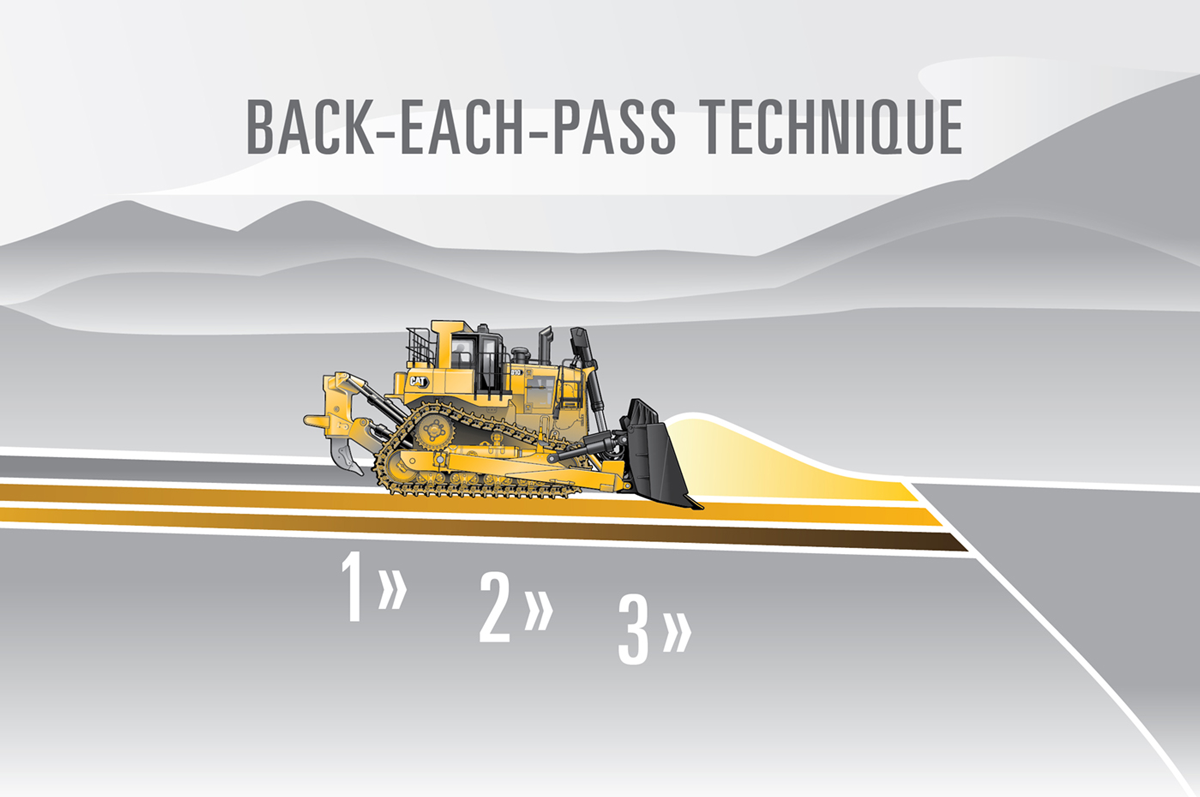
Back-to-Front Technique — Less Efficient
With this technique, commonly found in stockpile applications, the operator progresses the cut from back to front, so push distance is reduced with each pass as the dozer works to the front of the cut. However, efficiency suffers from uphill blade loading and the slot is not fully utilized throughout the cut.
“Even though you’re pushing shorter distances than back-each-pass, you’re pushing uphill and not using a slot from the blade to keep the blade fully loaded, which often creates windrows that will need to be cleaned up later,” says Metz. “Pushing uphill reduces productivity while increasing fuel burn.”
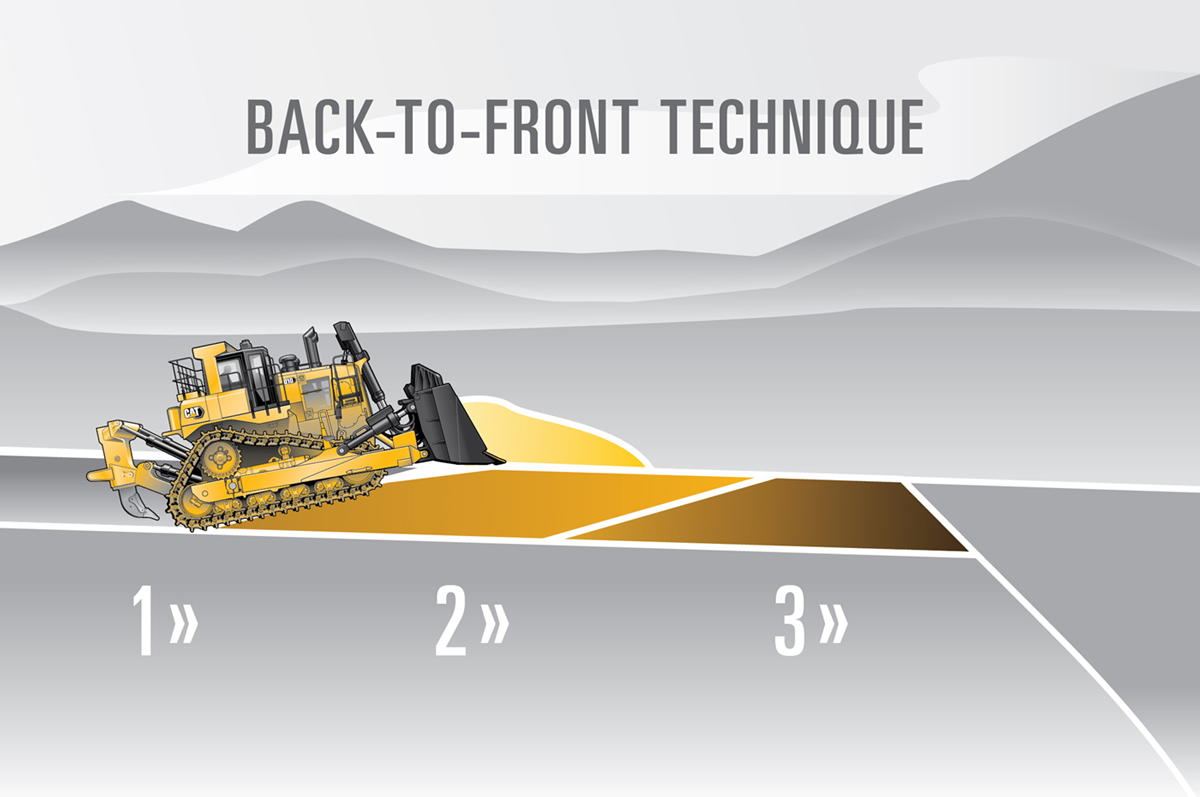
Front-to-Back Technique — Most Efficient
With this technique, the operator starts at the front of the cut and works to the back of the cut, and the push distance increases with each pass. This approach enables more efficient downhill blade loading, and the slot is created and utilized throughout the whole cut.
“After the first couple of passes, you’re going to create that slot in front of you, and that will help hold the material in front of the blade so you don’t have spillage or windrows,” says Metz. “You’re going to use the weight of the machine to help load the blade more quickly while having a shorter push distance.”
Push distance is a key metric when measuring dozer productivity. The average push distance on this technique is about half of the distance from the back-each-pass technique. A longer push distance requires a lot of time spent in reverse, which is not productive.
“With front-to back-dozing, we’re going to cut down on the amount of time we spend in reverse because we are basically going to stair-step back our passes,” he explains. “The carry portion of the cycle gets longer and longer each time.”
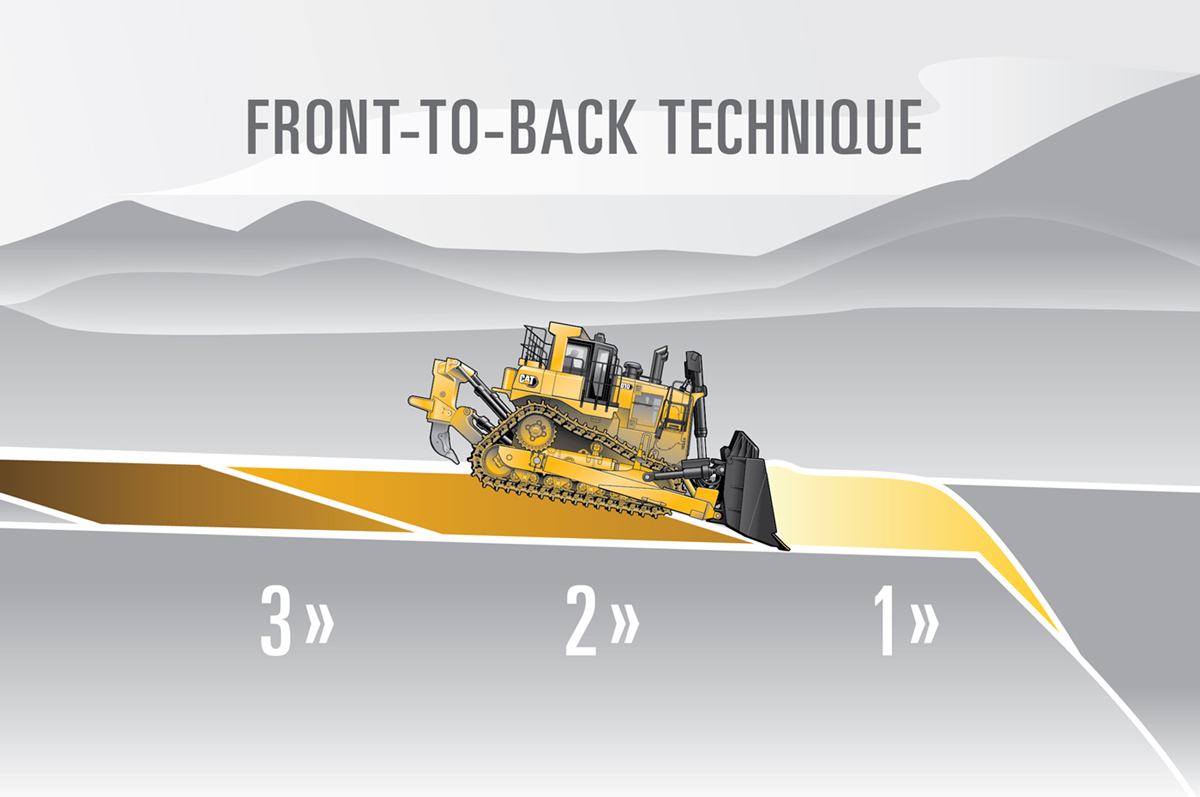
Big Load Slow Vs. Small Load Fast
Which technique is more productive — pushing a big load slow or a small load fast? Metz provides the answer:
“A dozer that takes a large load slowly will out-produce one that takes a smaller load faster. You can only push so much material in a higher gear. For example, you would have to do four passes in second gear to push the same amount of material you could push in three passes with the dozer in first gear. With small-load-fast, you’re spending more time in reverse and you’re not pushing full loads. This is why we teach first-gear pushes for large dozers.”
Metz shares this analogy: “Let’s look at it this way. If you had to move your entire household across the country, would you rather do it in one big trip with a large semi load, or would you rather do it in several smaller trips using several box trucks? One big semi load is obviously more efficient.”
LEVERAGING AUTOMATION
Advanced technologies like Automated Blade Assist (ABA) and AutoCarry™ can help Cat large dozer operators maximize the productivity of the dozing operation.
ABA increases efficiency while reducing operator workload. It comes standard with a dual-tilt configuration that automates the movement of the blade to three key preset pitch positions. The positions of each segment — load, carry and spread — can be set through an Information Display or the push-button keypad.
“With ABA, operators can load the blade and then tilt it all the way back to act as a bucket or scoop that carries the material. This puts more downward force on the blade, effectively making the dozer heavier,” says Metz. “When you do that, you can push more material and gain more tractive effort on the machine before it slips out.”
“Then, when you get to that dump cycle, the operator can tilt the cylinders all the way forward to dump the material, helping to clean off the blade and minimize carryback material.”
For more information, visit Cat.com/miningdozers.